The new welding robot from IGM is one of the largest in Europe. It has a 4x4x10 metre working area and capacity for weights up to 20 tonnes.
The investment of just over SEK 9 million will further reinforce Kiruna Wagon’s position as a supplier of the most cost-efficient products for transporting iron ore. By taking advantage of the quality enhancement effects offered by the robot welder, Kiruna Wagon aims to surpass existing requirements and expectations.
“Kiruna Wagon’s successful wagon production has enabled this investment, which also reinforces our opportunities to venture into new areas”, said Peter Nyström, welding engineer at Kiruna Wagon.
The large size of the robot is necessary in order to perform the demanding welding tasks on ore wagon F050 manufactured for LKAB. The 750-metre long trains consist of 68 wagons and weigh 8,500 tonnes. Each individual wagon is subjected to extreme tensile force, which burdens materials and seams. Precision robot welding enables more consistent welding quality and stronger bonding. A wagon supplied today should be able to carry 1.4 million tonnes of iron ore over the course of its 20-year lifespan.
IGM welding robot advantages:
- The welding robot utilises materials optimally, which means that 30 kg per wagon of welding wire can be saved, this allows LKAB space for an additional 9,000 tonnes of iron ore per year destined for the ice-free port of Narvik.
- Fixtures enable the body to be rotated during the entire welding process.
- Through programming, the desired consistency and high level of quality is achieved with welding speeds up to 80 cm per minute.
The welding robot was installed and calibrated by staff from IGM and IGM Nordic.
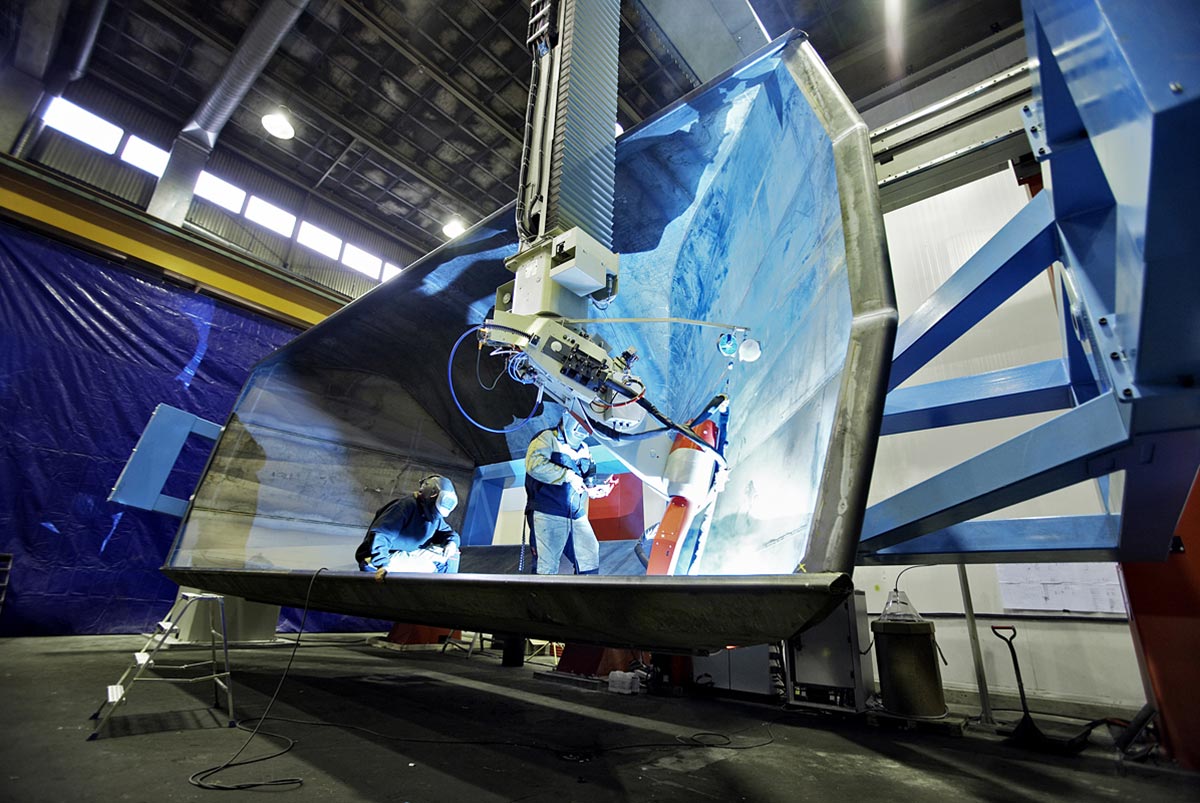
The investment in a welding robot will further reinforce Kiruna Wagon’s position as a supplier of the most cost-efficient products for transporting iron ore.